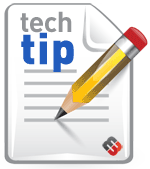
Condensation curing silicones can be broken down into two types: one part systems that are used, as is, and two part systems that require mixing. All condensation curing silicones require moisture to cure. One part systems get their moisture from the ambient environment. Two part systems typically contain enough moisture within them to cure once combined with a catalyst. Additionally, both types of systems need a path for the release of curing by-products, such as acetic acid, alcohol or acetone, or they will not readily cure.
For one part condensation silicones, increasing the humidity will speed the curing process. A particularly desirable cure cycle for silicone adhesives/sealants involves exposure to 130-150°F and 95-100% relative humidity. For two part systems, different catalysts are available to adjust for various cure schedules and thicknesses.
Keep in mind that with one part, condensation type silicones, thinner cross sections cure faster than thicker ones, with an 1/8 inch thick section typically curing within 24 hours. The catalyst in two part systems aids them in curing in sections up to 1 inch thick.
Master Bond Inc. has developed several specialty one part silicone adhesives.
MasterSil 711, when applied in thin sections, solidifies in 3-5 minutes and cures significantly faster than commercially marketed, competitive products. It is also non-corrosive to electronics and other sensitive elements.
MasterSil 713 is a very low viscosity, non-corrosive silicone which can be used as a coating or encapsulation material.
MasterSil 800 is a high temperature resistant, non-corrosive silicone for service up to 300°C (572°F).